CNC Plasma Cutting Machines: The Future of Metalworking
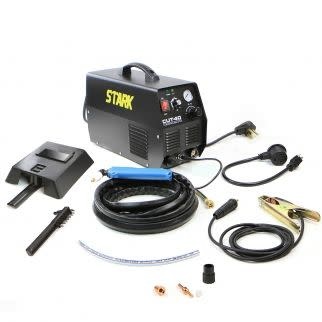
The metalworking industry is currently undergoing a transformational change, thanks to the introduction of computerized numerical control (CNC) plasma cutting machines. These machines have revolutionized how manufacturers produce metal parts, with many realizing benefits that were not possible before.
CNC plasma cutting machines have become the preferred tool for cutting metal sheets and plates. The machines use high-velocity plasma jets to cut through metals accurately and quickly, allowing for perfect cuts with no burrs or rough edges. The accuracy of CNC technology ensures that every cut is precise, increasing the efficiency of the manufacturing process.
Cutting metal has never been easier, and CNC plasma cutters have the unique ability to create complex shapes with ease, something that other cutting methods cannot achieve. The speed and accuracy of these machines also means that manufacturers can create prototypes faster and with less waste.
One company that is at the forefront of CNC plasma cutter innovation is a manufacturing company founded in August 2002, boasting more than 70 employees and six technical centers. The company uses its expertise to design and manufacturing digital cutting machines, non-standard equipment, escalator assembly lines, and parts processing.
They uphold their business philosophy of integrity, unity, pragmatism, innovation, and sustainable growth. This company offers cutting-edge CNC plasma cutting machines that can handle a range of metal thicknesses and sizes, with varying cutting abilities. Their machines provide high precision, speed, and consistent results, ensuring their clients achieve their desired outcomes, ultimately delivering high-quality products.
What are the advantages of CNC plasma cutting machines?
1. High Precision
CNC plasma cutting machines have a high degree of accuracy. The cutting process is controlled by a computer and is precisely executed along predetermined paths, ensuring every cut is exact, without human error. This level of precision promotes perfect cuts, reducing the need for extensive finishing.
2. Superior Quality
When dealing with metalwork, the slightest mistake can result in costly errors. CNC plasma cutting machines create high-quality cuts that do not require further polishing, resulting in less waste material and significant cost savings. The improved quality increases efficiency in the manufacturing process, ensuring timely delivery of goods to clients.
3. Flexibility
CNC plasma cutting machines are versatile and can be programmed to cut different shapes, sizes, and thicknesses of metal. With additional software programs, manufacturers can modify the machine's settings to suit the project specifications, providing even more flexibility to meet client requirements.
4. Speed
CNC plasma cutters are incredibly fast and efficient, dramatically reducing production time compared to using traditional cutting methods. A CNC plasma cutter can identify an edge in seconds and adjust the cutting speed accordingly, saving time and resources for the manufacturer.
5. Safety
CNC plasma cutting machines have high-level safety features as they reduce the risk of manual cutting significantly. This ensures that the employees can operate with more ease and safety while also reducing the risk of injury in the workplace.
Conclusion
As CNC plasma cutting machines are becoming mainstream in the metalworking industry, they provide significant advantages over traditional cutting methods. The technology has improved the quality, speed, and accuracy of the manufacturing process, ultimately increasing efficiency for businesses. The CNC plasma cutting machine is at the forefront of manufacturing technology due to the machines' versatility, safety features, and flexibility. Companies that adopt and embrace this technology will have a better overall production experience, meeting their client's needs and creating consistent high-quality products.