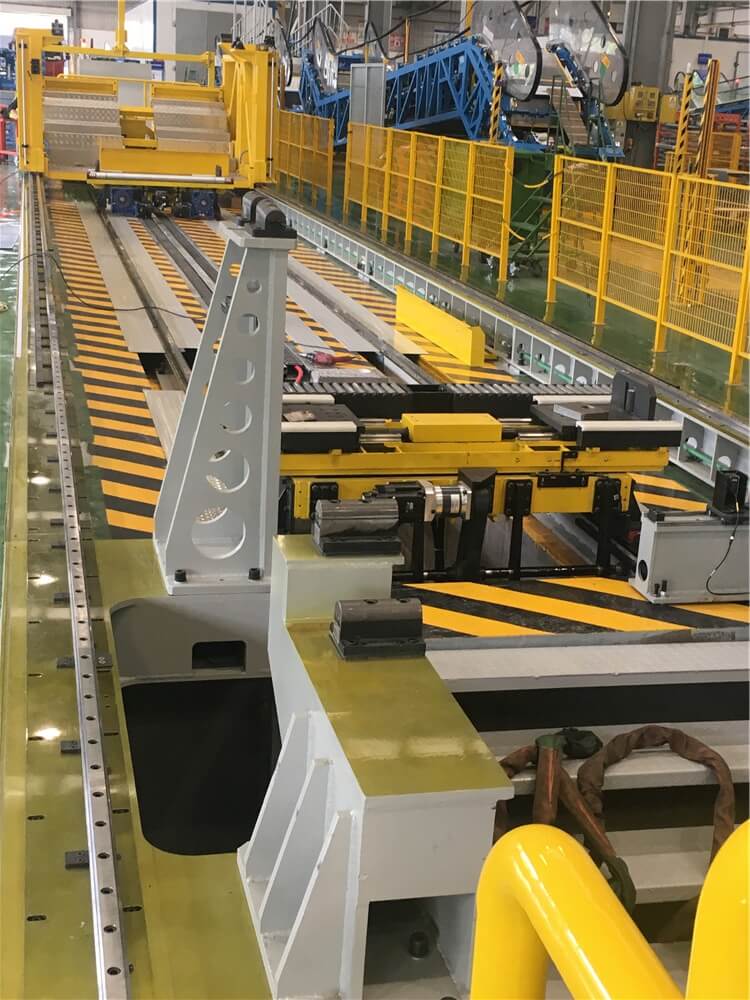
The production process of melt-blown fabric is intricate and requires a high level of expertise and technological capabilities. The company has invested in state-of-the-art equipment, including digital cutting machines, non-standard equipment design and manufacturing, escalator assembly lines, and parts processing machinery. This advanced technology has enabled the company to streamline its production process and enhance the quality of its melt-blown fabric.
Melt-blown fabric is a non-woven material that is produced using melt-blown technology. The process involves melting and extruding polypropylene, creating a web of fine fibers that are then stretched and cooled to form a fabric. This fabric is known for its ability to effectively filter tiny particles, making it an essential component in face masks and respirators. The demand for melt-blown fabric has surged in recent years, particularly in response to the COVID-19 pandemic, as the global need for face masks and PPE has escalated.
The company's expertise in digital cutting machines and non-standard equipment design and manufacturing has been instrumental in optimizing the melt-blown fabric production process. These technologies allow for precise and efficient cutting and shaping of the fabric, ensuring that it meets the required specifications for use in medical-grade face masks. Additionally, the company's escalator assembly line and parts processing capabilities contribute to the seamless production of melt-blown fabric, further solidifying its position as a leading manufacturer in the industry.
Innovation is at the core of the company's operations, driving continuous improvement and the development of new and advanced techniques for melt-blown fabric production. The company's technical centers play a pivotal role in research and development, constantly exploring innovative methods to enhance the quality and efficiency of the production process. By staying at the forefront of technological advancements, the company is able to meet the evolving demands of the market and uphold its commitment to producing high-quality melt-blown fabric.
Furthermore, the company's commitment to sustainable growth is evident in its approach to manufacturing and operations. As the demand for melt-blown fabric continues to grow, the company remains dedicated to minimizing its environmental impact. This includes implementing energy-efficient practices, reducing waste, and prioritizing sustainable materials in the production process. The company recognizes the importance of balancing economic growth with environmental consciousness, and has made it a priority to operate in an environmentally responsible manner.
In conclusion, the company's investment in advanced technology, combined with its commitment to innovation and sustainable growth, has positioned it as a leader in the production of melt-blown fabric. The company's proficiency in digital cutting machines, non-standard equipment design and manufacturing, escalator assembly lines, and parts processing has enabled it to meet the surging demand for high-quality melt-blown fabric, particularly in the context of the global health crisis. Moving forward, the company remains dedicated to driving innovation and maintaining its excellent standard of production, ensuring that it continues to be a key player in the manufacturing industry.